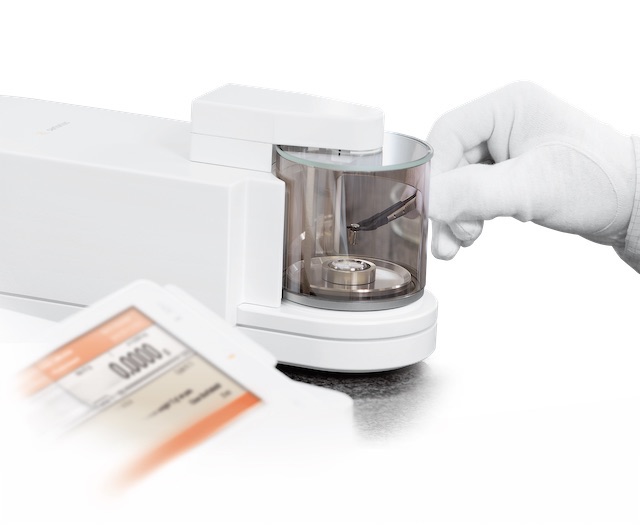
This article offers an obvious and straightforward explanation of IQOQ concepts.
In the highly-regulated pharmaceutical, clinical, and medical industries, even minor inconsistencies can become severe problems without the correct qualification and validation protocols set in place. As a quality assurance component, equipment validation is crucial for producing consistent, high-quality products. One of these key sets of protocols within equipment validation is Installation Qualification (IQ), Operational Qualification (OQ), and Performance Qualification (PQ).
This article offers an obvious and straightforward explanation of these concepts, why they’re important, what makes them so successful, and a model for connecting with different professionals who can plan and execute these kinds of projects. To learn about IQOQ and its relation to the lab, read on!
What is IQ, OQ, and PQ?
IQ, OQ, and PQ protocols are methods for fully demonstrating that the equipment being used or installed will offer a higher degree of quality assurance such that the production process will manufacture products that meet their quality requirements. It is essential to understand these concepts since they’re a bit complex.
Installation Qualification (IQ)
Newly installed and modified equipment must first be validated to determine if it can produce the desired results through some Design Qualification (DQ for short), a protocol defined as the set documented verification of a proposed design’s ability to meet the requirements it must fulfill. But how a particular hardware or software unit works in real-world scenarios depends a lot on the installation procedure. Installation Qualification verifies that an instrument or team of equipment being qualified has been installed and configured by the manufacturer’s specifications or installation checklist.
Operational Qualification (OQ)
Operational qualification is performed after meeting every protocol of IQ. OQ’s primary purpose is to determine that equipment performance is consistent with user requirement specifications in the manufacturer-specified operating ranges. This means identifying and inspecting the equipment features that could impact the final product quality.
Performance Qualification (PQ)
The final step of qualifying equipment is with PQ. During this phase, the qualification and validation team will verify and then document that the user requirements are being verified. The user requirements should include the normal operating range. Once you have qualified the equipment, you can develop each process required for every product. Then, once each method is developed fully, it can then be validated. Instead of testing each component and instrument one by one, the PQ tests them all as a partial or overall process.
FOR ALL ISO 17025 CALIBRATION SERVICES, CONTACT LAB PEOPLE TODAY
Lab People Inc. is a trusted provider of laboratory equipment, services, supplies, and rental equipment for you and your laboratory. As an ISO 17025 accredited service organization, we stand behind our services with 100% satisfaction guaranteed for all our customers. We offer on-site and off-site calibration services for balances, pipettes, moisture analyzers, force measurement, test weights, and more. Services include preventative maintenance, SQ-Min, IQOQ, repairs, legal for trace/placed in service, verification, and more.
For more information about how we can assist you, visit our website, email us, or call us at 1-800-296-2001!